Steel Water Pipe
STI/SPFA members are involved in standards development activities and have written several design manuals, developed design software, and are actively involved in research projects testing joint efficiencies and recommending coating procedures on internal welds after backfill is in place.
Find an STI/SPFA fabricator member for your next water pipe project.
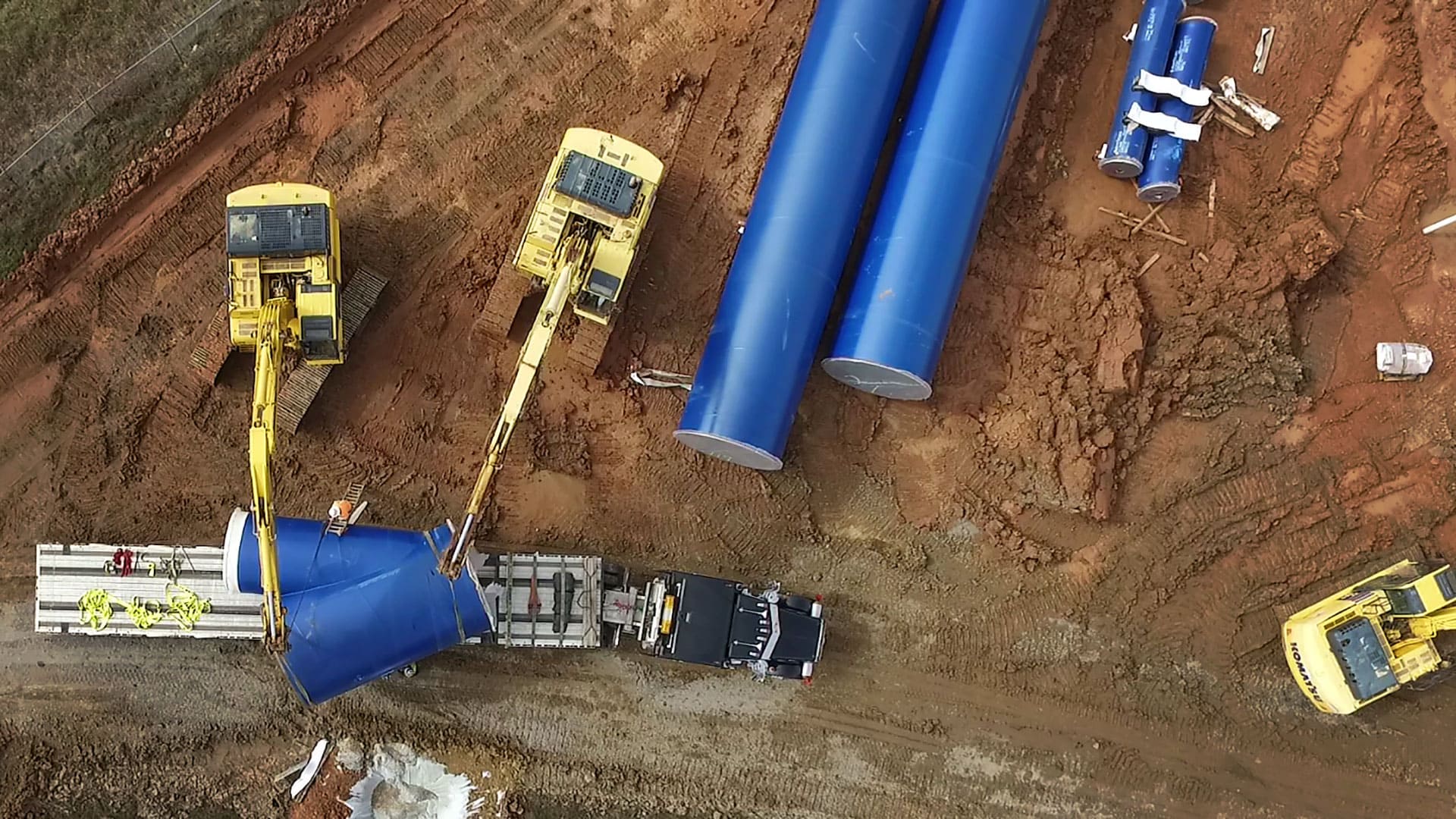
The 5th Edition of AWWA M11 Pipe Design Clarified
This series of articles was developed to point out important changes in the new edition of the AWWA M11 Steel Pipe.
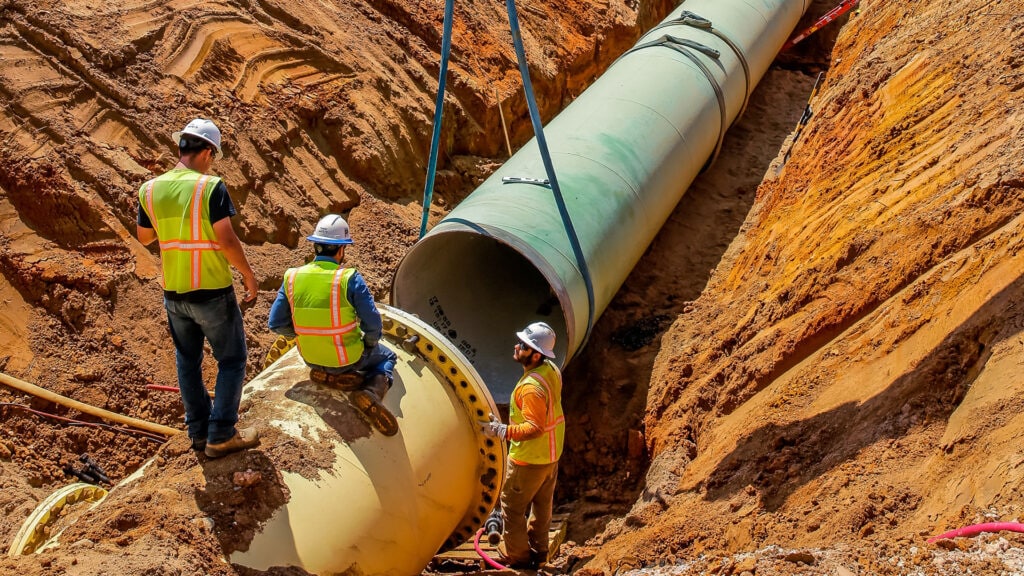
Suggested Specification for Buried Steel Water Transmission Pipe
This steel pipe specification gives guidance on the products, design, and installation as they relate to buried steel water transmission pipe.
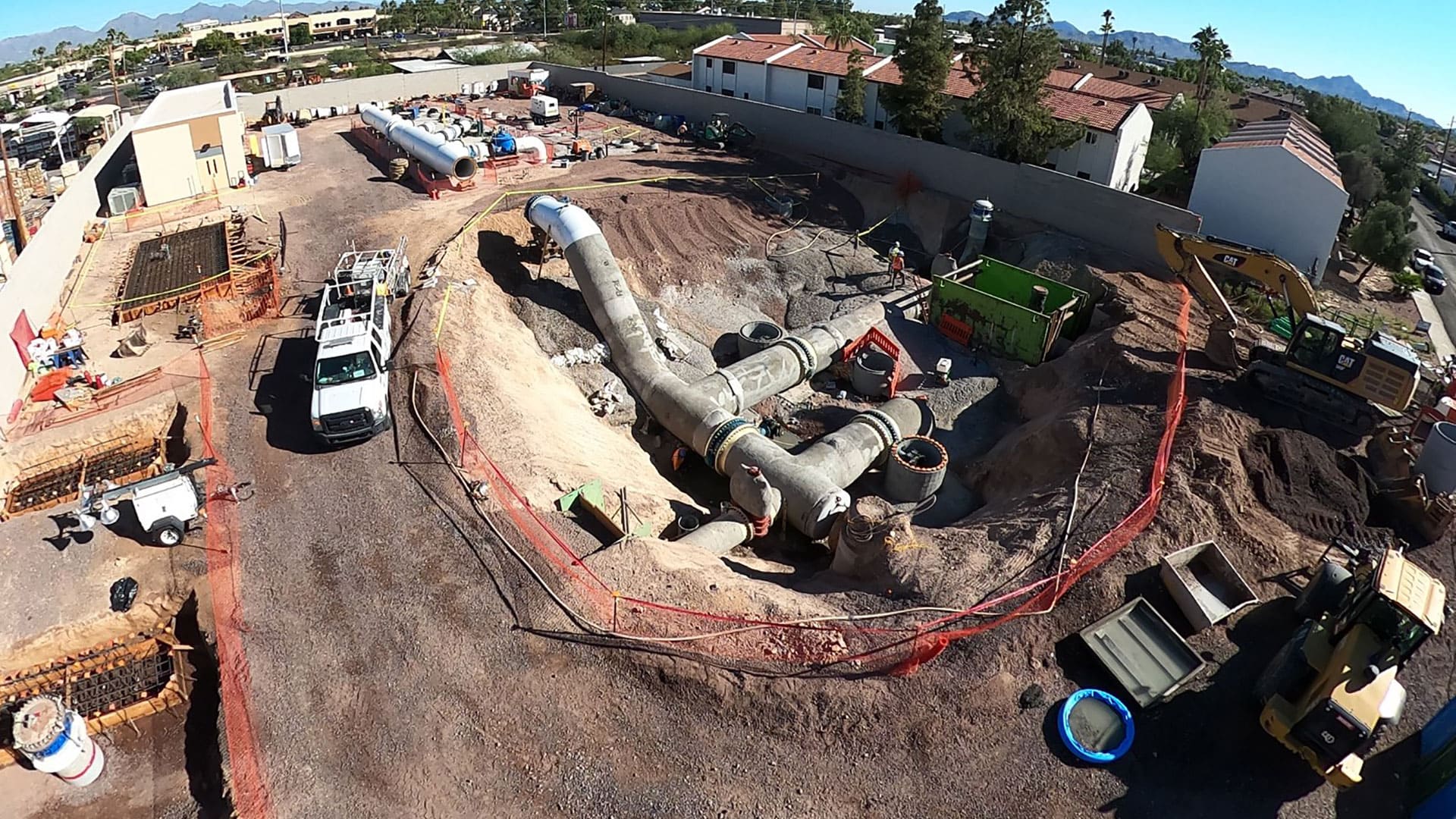
Safety Factors in AWWA Water Pipe Design
Historically, safety factors have been used as a measurement of safety versus failure. But how safe are these values for the final design?
EDUCATION
SPFA Pipe Quality Certification Program
The SPFA Pipe Quality Certification is a requirement in most piping specifications in the United States water transmission industry. The program addresses quality assurance and control, lining and coating operations, and equipment and welding procedures specific to steel water piping. The certification process also evaluates a company’s management, organization, engineering and procurement practices.
EDUCATION
Steel Pipe Tech Library
STI/SPFA members have written several design manuals, presented technical papers addressing important issues, and are actively involved in research and development projects.
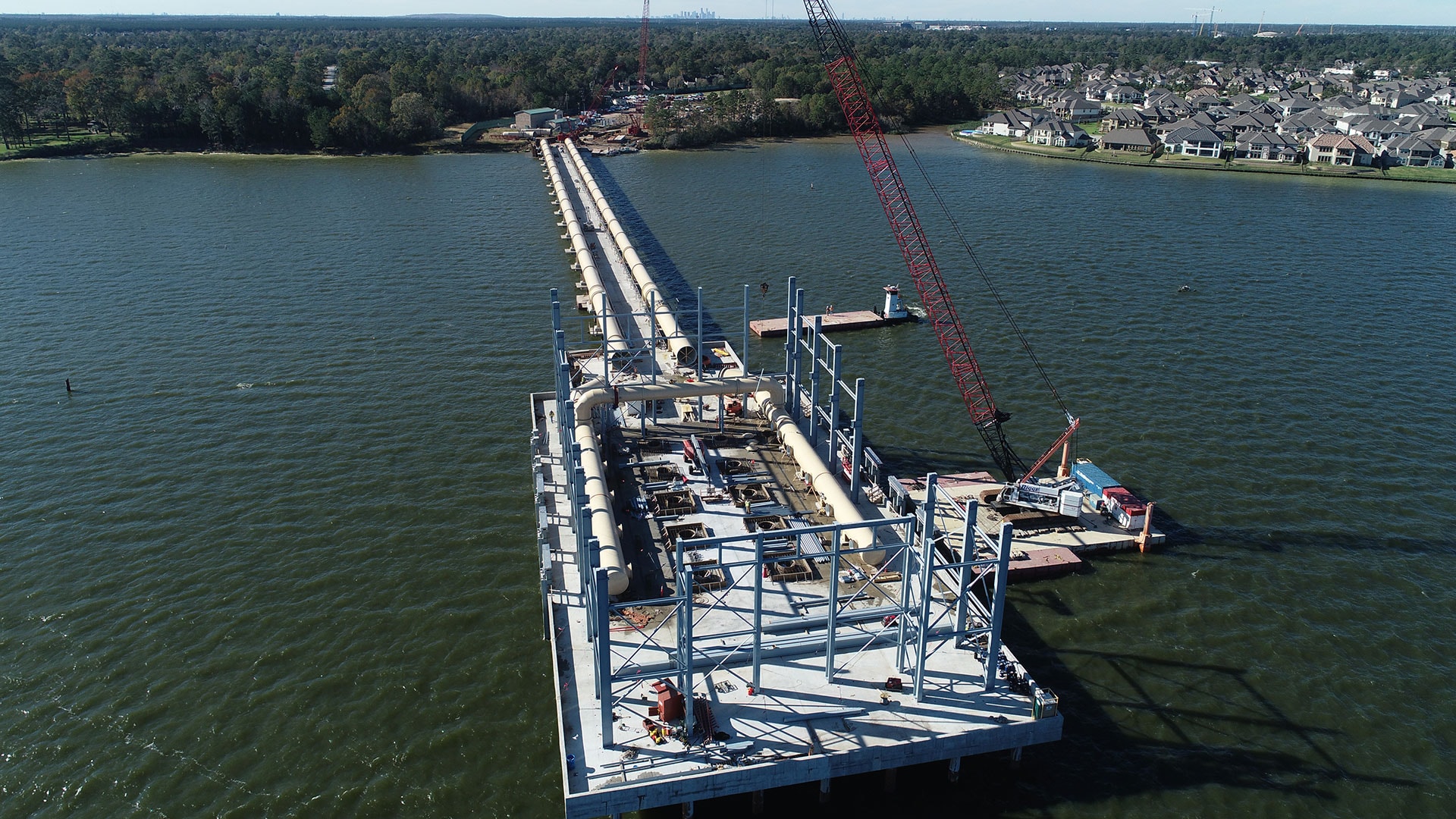
The Steel Tank Institute/Steel Plate Fabricators Association presents awards each year to commend outstanding records in quality of product, safety achievements at member facilities, and outstanding projects completed by members.
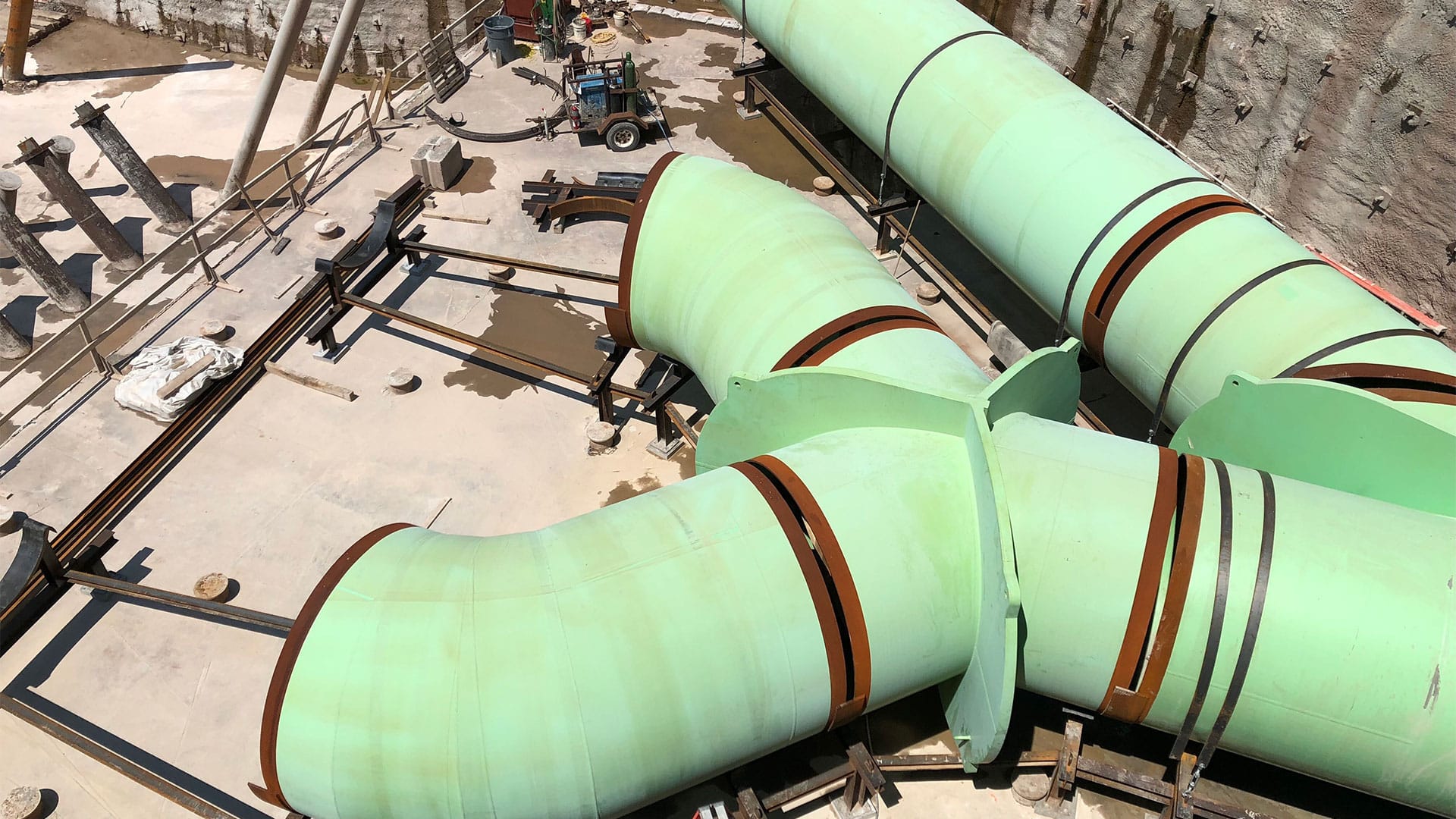
The STI/SPFA Steel Water Pipe Section members created a presentation to educate you and your customers on the use and benefits of steel pipe.