In order to safeguard your business, maintain good customer relations, ensure high-quality fuel, and leak-free operation of your storage systems, you must monitor for water in those systems and remove water whenever it is detected.
This must be a routine part of your operations and maintenance procedures. The EPA states that a new or upgraded UST system is a good start, but the system must be properly operated and continuously maintained. This includes water monitoring and removal.
Water Monitoring and Removal is Critical for All Storage Systems
Poor operations and maintenance procedures for water monitoring and removal from storage systems can lead to a number of problems, from degradation of fuel quality and subsequent vehicle performance, to microbial contamination and damage of the entire storage system.
This pertains to all storage systems, both underground and aboveground, constructed of any material and storing nearly any product – gasoline, diesel, residential and commercial heating oils, aviation jet fuel and others.
The entire storage system is potentially impacted by water and its possible consequences, not just the storage tank. While the tank, as the common collection place, is where chemical reactions can brew, it also provides an easy means to monitor for water in the system and a common place to treat the problem.
It is imperative that all owners and operators of storage systems immediately implement routine operations and maintenance procedures for water monitoring and removal of water, if detected.
Recent Industry Changes Elevate the Importance of Water Monitoring and Removal
Although operations and maintenance procedures for water monitoring and removal have been a recommended practice for over thirty years, recent changes within the industry have increased the risk for water entry and accumulation in the storage system, and subsequent microbial growth if water is not removed.
The Distribution Infrastructure
More fuel is moving faster through the distribution/delivery infrastructure, leaving less time for water to settle out before the product moves from step to step in the distribution process. A shift from proprietary to shared delivery infrastructures (bulk terminals, pipelines, transports) has removed much of the control that individual companies had over the process and product.
Gasoline Chemistry
From the removal of lead and MTBE, to additives such as ethanol and biodiesel, product chemistry has undergone fairly recent change. These new fuels are more susceptible to moisture accumulation, separation and potential biodegradation accelerated by water. For example, lead was a natural poison to the microbes that could grow in a moist environment – in today’s lead-free fuels, microbial growth can more readily occur.
Installation Procedures
Common procedures – including open vents, low fill areas and sloped tank installations – contribute to water accumulation.
Microbial Activity
Microbial activity is better understood and more common. As a result of the above changes within the industry, microbial activity has been found to be a much more common phenomenon than previously realized.
How Water Enters a Storage System
In addition to possible water in the delivered product, water can enter a storage system via damaged fill boxes or fill cap gaskets, loose fittings or plugs, poor practices relating to spill buckets, rainwater accumulated within tank sumps and which enter via any tank orifices that are not water/vapor tight, and condensation caused by fuel temperature swings or air entering via vents. Certain fuels are also more prone to moisture attraction and subsequent separation when subject to temperature swings.
Preventing Potential Problems Associated with Water
Major industry groups have developed recommended operations and maintenance procedures, but basic practices include:
- Monitoring and checking for water with automatic tank gauging systems and manual gauge sticks.
- Inspecting fill and vapor caps for damages and for missing gaskets, replacing if necessary.
- Inspecting product and spill containment buckets and proper disposal of water if found (not draining back into the tank).
- Auditing the fuel delivery process and water content.
- Using water-sensitive fuel filters and watching for slowed-down fueling.
- Treating storage tanks with antimicrobial pesticide (biocide) on a regular basis.
- Employing a qualified professional to examine the inside of the tank, remove any water and sludge, and clean the tank periodically.
Locating and Removing Water in a Storage Tank
The first point of contact for guidance is a petroleum equipment or services contractor and/or the fuel supplier. Additional guidance is available from organizations such as:
- American Petroleum Institute (API)
- Petroleum Equipment Institute (PEI)
- ASTM International
- National Oilheat Research Alliance (NORA)
Manual tank gauging and/or automatic tank gauging can detect water, but periodically pulling product samples from the tank is a prudent practice. Samples should be taken from the low end of the tank and if possible, from more than one location in the tank. Hazy or waxy fuel samples indicate water and readily available field detection kits can check for microbes and whether the fuel meets specifications.
If water is detected at any time, it must be removed by qualified service contractors.
Signs of Microbial Growth
Plugged fuel filters are a common result of microbial growth, caused by the slime created by a thriving microorganism colony clogging the small filter openings. Filter life shorter than six months is a warning signal (when flow slows to 3-5 gpm, something is amiss). Other signs are plugged fuel lines, erratic gauge readings, a rotten-egg odor, and frequent replacement of other components such as valves, rubber seals and hoses. Problems may also surface in vehicles fueled by contaminated product, such as plugged fuel filters and unusual exhaust smoke. If water levels in a storage tank were high enough to be pumped directly into a vehicle, immediate and major problems would occur – this is of particular concern when switching to ethanol-based fuels.
Field detection kits can verify microbial growth, but it is suggested that qualified professionals with expertise in microbial contamination control be contacted to develop a treatment plan. This may include initial tank cleaning to remove the slime and sludge, followed by a treatment with a biocide.
Additional Information
Contact your fuel supplier and/or a petroleum equipment or service provider. Standards and informational resources are also available from organizations such as the STI/SPFA, EPA, API, PEI, ASTM, PMAA, NORA, DOE, and your state or local authorities.
Frequently Asked Questions
Why the concern about water in a storage system?
Poor operations and maintenance procedures for water monitoring and removal from storage systems can lead to a number of problems:
- Gasoline or diesel fuel quality can be degraded and result in poor performance of vehicles, failed exhaust emissions, or even major engine damage.
- Filters can become prematurely plugged and lead to excessive maintenance and replacement costs.
- Plugged filters also slow down fueling and reduce throughput and sales for retail facilities.
- Users become dissatisfied and retail facilities can lose customers.
- Microscopic bacteria can grow in a moist environment and attack the entire storage system, including steel and fiberglass reinforced plastic tanks, tank linings, elastomeric seals and hoses, low points in the piping, leak detectors, turbine pump components, filters and valves, including overfill prevention devices.
- In the worst case, product leaks can cause environmental damage, leading to costly cleanup and facility downtime/lost business.
Is the concern about water relevant only to underground storage systems?
No. Similar operations and maintenance procedures for water monitoring and removal should be implemented for aboveground storage systems, even small residential Number 2 heating oil tanks.
Does the concern about water pertain only to gasoline or diesel fueling systems?
No. Nearly all stored products can be adversely affected by the presence of water. An extreme example is aviation jet fuel, where water in the product has obvious harmful consequences. But even heating oil systems are subject to problems caused by water. The presence of water in fuel oil can cause oxidation, a natural chemical process that breaks down the fuel oil and forms insoluble particulates, commonly called “sludge”. This sediment can clog fuel lines, nozzles, filters and screens – and ultimately lead to wear in pumps and system malfunction. Consequences include unhappy customers, increased service calls, and unnecessary added costs.
It should also be noted that at facilities with lower product throughput – such as commercial or industrial sites and lower-volume service stations – water has greater potential for accumulation.
How does water get into a storage system?
Water can enter a storage system in a number of ways, including:
- Condensation, caused by air entering via the vents or fuel temperature swings (especially aboveground tanks).
- Damaged spill bucket or fill cap gaskets.
- Loose fittings or plugs.
- Allowing water captured in a spill bucket to be drained into the storage tank.
- High throughput in the fuel distribution/delivery infrastructure, allowing less time for water to settle out of the product before it’s pumped at the refinery or as it’s moved along the shipping process.
- Certain fuels are more prone to moisture attraction and subsequent separation when subject to temperature swings. A fuel’s aromatic content and temperature affect the amount of moisture it can hold. Generally, the higher in aromatic content and the warmer the fuel, the more water it can hold in solution. That’s usually not a problem until the fuel is cooled, causing the water to be released and settle at the bottom of a storage tank.
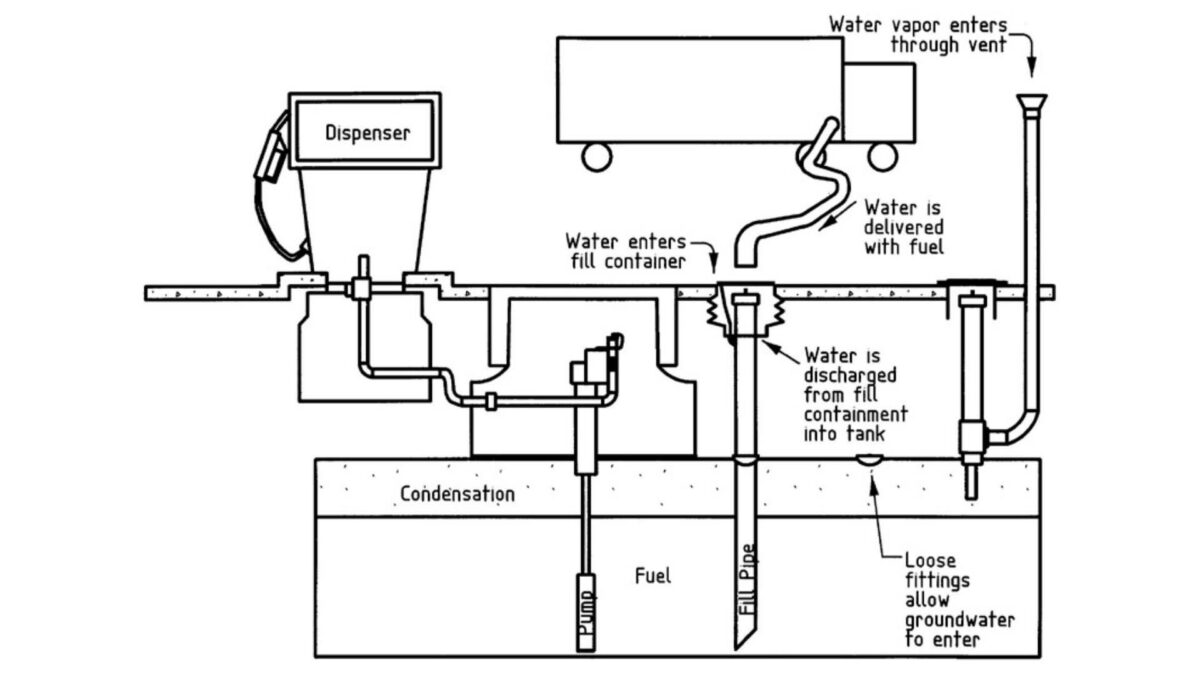
Possible Water Entry Points Into a Storage System
Hasn’t water always been possible within a storage tank? Why the concern today?
Operations and maintenance procedures for water monitoring and removal have been a recommended practice for over thirty years. However, a number of things have changed over the past few years that have increased the risk for water entry and accumulation in the storage system – and subsequent microbial growth if water is not removed.
Today’s distribution/delivery infrastructure is different from only a few years ago. Terminal capacity in the United States has been shrinking yet fuel consumption has continued to grow. As a result, more fuel is moving through distribution at a faster rate, leaving less time for water to settle out before the product moves from step-to-step in the distribution process. Also, as the industry has moved from proprietary to shared delivery infrastructures, individual companies have less control over the process and product.
Gasoline chemistry has changed significantly, from the removal of lead and MTBE, to additives such as ethanol. Most of these changes were done to comply with standards set by Fuel and Fuel Additive Regulations (40 CFR 79) that became effective in 1996. These new fuels are more susceptible to moisture accumulation, separation and potential biodegradation accelerated by water. For example, lead was a natural poison to the microbes that can grow in a moist environment – in today’s lead-free fuels, microbial growth can more readily occur. With alcohol-enhanced fuels, “phasing” can more easily occur, separating water, gasoline and alcohols into three distinct layers.
Common installation procedures – including open vents, low fill areas and sloped tank installations – contribute to water accumulation.
Most of these are conditions that did not exist in the 1970s, 1980s, or even much of the 1990s – certainly not to the extent that they exist today. Furthermore, microbial activity is better understood today and has been found to be a much more common phenomenon than previously realized. Owners and operators of storage systems need to be aware of these problems and immediately implement operations and maintenance practices to monitor for and remove any water from storage tanks.
“Being new or upgraded is not enough…Having a new or upgraded UST system is a good start, but the system must be properly operated and continuously maintained.”
U.S. Environmental Protection Agency “Operating and Maintaining Underground Storage Tank Systems: Practical Help and Checklists” (EPA 510-B-00-008), 8/2000
Is it only the storage tank where water is a concern?
Absolutely not. The entire storage system is potentially impacted by water and its possible consequences. The storage tank, naturally, is the repository for the entire system contents – subsequently, it essentially functions as the cauldron where such chemical reactions can brew. However, on the plus side, the storage tank provides a communal place and an easy means to monitor for water in the system – and subsequently provides a common place to treat the problem.
What can be done to prevent problems associated with water in a storage system?
You must establish operating and maintenance practices to monitor for water and remove water when it is detected. Major industry groups have developed recommended operations and maintenance practices (see References and Resources section), but common practices include:
- Monitoring and checking for water. An automatic tank gauging (ATG) system with water monitoring capability is an ideal method, as long as the sensors are maintained to be functional. However, simple manual monitoring with alcohol-compatible water paste on a gauge stick is a quick, easy and inexpensive way to check for the presence of a water bottom in your storage tank.
- If water is detected in the bottom of the tank, remove it.
- Inspect fill and vapor caps for damage and missing gaskets, replacing if necessary.
- Inspect product and spill containment buckets – if water is present, do not drain it into the tank but instead, remove and properly dispose of the water.
- Audit your fuel deliverer’s tank filling process and request that water content be included on the delivery Certificate of
- Analysis. Measure water level before and after each fuel delivery.
- Ask your fuel supplier what measures are taken to ensure fuel is delivered without water.
- Use water-sensitive fuel filters and watch for slowed-down fueling – this may be a sign of a problem.
- Treat your storage tanks once or twice a year, or as needed, with a “maintenance level” dosage of antimicrobial pesticide (also called biocide), products that disinfect fuels and fuel systems. Make sure these are EPA-approved and that you contact a supplier who is knowledgeable about treatment protocols and handling.
- Examine and maintain the inside of the tank using professional contractors, removing any water and sludge.
As an added safety measure, have the tank periodically cleaned by qualified professional contractors.
Such practices should be conducted by every owner/operator of storage systems, but certain installations may be even more susceptible to water accumulation, such as low throughput service stations, fleet fueling sites and other commercial or industrial UST or AST sites. The less a storage and dispensing system is used, the easier water can accumulate in the system.
What is the procedure for locating water in a storage tank?
You should first contact your petroleum equipment contractor and/or fuel supplier. They could tell you what monitoring devices may already be installed on your storage system, provide guidance on operations and maintenance procedures, and advise you on additional steps you should take.
Additional guidance on procedures for water monitoring and periodic sampling is available from organizations such as the American Petroleum Institute (API), ASTM International, and the National Oilheat Research Alliance (NORA).
Simple manual tank gauging, using alcohol compatible water paste on the gauge stick, is one method of checking for water bottoms. Also, most automatic tank gauges (ATGs) can detect water, but you must ensure that the water sensors are maintained to be functional. In fact, some guidelines suggest comparing the product level reading taken with a manual tank gauge with that on your ATG – discrepancies may indicate water.
How often should you check your storage tank(s) for water?
As frequently as possible. In fact, some major oil companies require station operators to check daily for water bottoms.
In addition to the simple procedures outlined above, you should also pull periodic product samples from the inside tank bottom and inspect them. Check with your petroleum equipment dealer or fuel supplier for guidance on sampling devices and procedures. Some basic guidelines include:
- Pull samples from the low end of the tank – tanks are often installed with a slight tilt to allow for water to collect in the sump.
- Be aware of the pitfalls of using the fill tube as the sampling port – if it is not located at the low end of the tank, sludge or water may not be detected. Also, if the fill tube is not installed straight, water and sludge may not be detected or it may appear that there is less quantity than there really is.
- If possible, samples should be taken from more than one location in the tank.
If the fuel sample looks hazy, or waxy in cold weather, water is probably present. A field detection kit, available from petroleum equipment suppliers, can then be used to check the fuel for the presence of microbes and whether the fuel meets the appropriate fuel specification such as ASTM D396 or D975. Independent labs can conduct in- depth analysis to determine the extent of any microbial contamination.
If water is detected at any time, you must have the water removed from the tank and disposed of properly, using contractors with expertise. You should also inspect the storage system for obvious points of water entry, such as damaged fill boxes or loose fittings, and replace defective components.
If water accumulation is an ongoing problem, consider using periodic treatments of antimicrobial pesticide (biocide) for the fuel and fuel system as an added safety measure.
How can I tell if microbial growth is occurring in my storage tank, and what can be done if it is?
A number of providers can help you determine this, but there are also field detection kits available from petroleum equipment suppliers (see discussion in above section). But there may be simple signs of microbial growth evident in day-to-day operations – for example, plugged fuel filters. As microorganisms begin to thrive and grow, these “bugs” form into slime, which breaks off and clogs small openings throughout the entire system, especially filters. Filter life shorter than six months is a warning signal (when flow slows to 3-5 gpm, something is amiss).
It may be helpful to compare this phenomenon with mold, which also thrives in a moist environment, begins growing microscopically unseen to the human eye, but eventually becomes a visible, tangible substance.
Other clues of contamination include plugged fuel lines, erratic gauge readings, and frequent replacement of other components such as valves, rubber seals and hoses. You might even smell a foul rotten-egg odor because as the bugs digest fuel, they alter it chemically to produce sludge and other materials that attack metal, rubber, fiberglass reinforced plastic, tank linings and coatings. If the slimy bugs reach engine fuel systems, they can plug fuel filters and cause build-up around the injection nozzles, resulting in inefficient combustion (or none at all) and unusual exhaust smoke.
So what do you do if microbial growth is suspected or detected? Contact a qualified, reputable professional with expertise in microbial contamination control (see References and Resources section). They will work with you to develop the best plan of attack. Heavily contaminated storage systems will most likely require cleaning to remove the slime and sludge, followed by a treatment with a biocide.
I’ve heard that ethanol gasoline and biodiesel can cause problems relating to storage system corrosion. Is this true?
Complications can arise using either of these materials, but for different reasons.
Ethanol
Ethanol is incompatible with certain reinforced plastic materials used before 1984, lining materials, and older adhesives, sealants and gaskets. In addition, ethanol blended fuels have reduced tolerance for water and therefore, water bottoms can be more problematic.
Water reacts differently in ethanol-blended fuels than it does in fuels that were oxygenated with MTBE. With MTBE, water immediately falls to the bottom of the tank. Ethanol-blended fuels can hold much more water – once the fuel is saturated with water, excess water will separate and cause two distinct layers of product. The top layer will be mostly gasoline that is lower in octane and perhaps out of specification, while the bottom layer is a mix of ethanol and water that will not burn. Further, it is in that water bottom where microbes can grow and proliferate and where the storage system is exposed to greater than 10% of ethanol.
Ethanol also tends to loosen any sludge, slime and scale that may already be present in a tank. Therefore, if these tanks are not cleaned before the ethanol-blended fuel is introduced, that material can be picked up and clog filters.
The bottom line when it comes to storage tanks and ethanol:
- Check for compatibility with all compositions of ethanol
- Clean the tanks before introducing ethanol-blended fuels
- Monitor for water frequently – and remove it when detected
Biodiesel
There are some material incompatibility issues with both diesel and biodiesel fuels:
- Brass, bronze, copper, lead, tin, or zinc, oxidizes both diesel and biodiesel fuels and creates sediments, which in turn can result in plugged fuel filters.
- Pure biodiesel (B100) or blends higher than B20 cause more problems with rubber seals, gaskets, and hoses – make sure biodiesel resistant materials are used.
For additional information go to the Clean Fuels Alliance America website.
Biodiesel can create further problems if it is introduced into a storage tank that previously held diesel. Number 2 diesel tends to form sediments that stick to and accumulate in storage systems, forming layers of sludge or slime – the older the system and the poorer the maintenance, the thicker the accumulation. Biodiesel, being a good cleaning agent, will dissolve these sediments and carry the dissolved solids into the fuel systems of vehicles. Fuel filters will catch most of it, but in severe cases the dissolved sediments can rupture filters and can cause fuel injector failure. B20 generally doesn’t create problems as much as higher blends or B100 biodiesel, but tanks should be cleaned before switching to any biodiesel.
Industry experts recommend that biodiesel meet ASTM D6751 and be used within six months of manufacture to ensure that the quality of the fuel meets specifications. Fuel degradation pathways for biodiesel are more likely with higher concentration blends due to the higher presence of the biodiesel, so stability concerns and issues are likely to be higher and may occur faster as the blend level is increased.
The bottom line when it comes to storage tanks and biodiesel:
- Check for compatibility
- Steel is compatible
- Clean the tanks before introducing biodiesel fuels
- Monitor for water frequently – and remove it when detected
Who can I contact for more information?
Your first point of contact should be your fuel supplier and/or a petroleum equipment or service provider. In addition, various standards and informational resources are available, including those listed in the References and Resources section of this document.
References
American Petroleum Institute (API)
1220 L Street, NW
Washington, DC 20005-4070
202-682-8000
www.api.org
The Filtration and Dehydration of Aviation Fuels – Sources of Dirt and Water – Methods of Detection and Removal – Maintenance of Equipment (API 1501, Revision 65). November 2000.
Recommended practices relevant to water monitoring and removal for aviation fuel systems.
Bulk Liquid Stock Control at Retail Outlets (API RP 1621, 5th Edition). May 1993 & Reaffirmed January 2001.
Recommended practices applying to underground storage of motor fuels and used oil at retail and commercial facilities, involving controlling stock losses, safety & pollution control to maximize profits.
Design, Construction, Operation, Maintenance & Inspection of Terminal and Tank Facilities (API Standard 2610, 1st Edition). July 1994.
Includes standards on pollution prevention and waste management, safe operations, fire prevention and protection, tanks, mechanical systems, product transfer and corrosion protection.
ASTM International
100 Barr Harbor Drive
P.O. Box C700
West Conshohocken, PA 19428-2959
610-832-9585
www.astm.org
Standard Guide to Microbial Contamination in Fuels and Fuel Systems. (D-6469). 1999.
A guide providing an understanding of the symptoms, occurrence, and consequences of chronic microbial contamination and the control of microbial contamination in fuels and fuel systems. Applies primarily to gasoline, aviation, boiler, industrial gas turbine, diesel, marine and furnace fuels.
Fuel and Fuel System Microbiology: Fundamentals, Diagnosis, and Contamination Control. (MNL-47). 2003.
A guide providing sampling strategies and techniques, recommendations for disinfecting and removing microbial contamination from fuels and fuel systems, and a variety of diagnostic tests. This is designed to complement Guide D-6469.
Practice for Manual Sampling of Petroleum and Petroleum Products. (D-4057).
Recommended procedures for sampling fuel that should become an integral part of a fuel quality program. Among other things, D-4057 states that (a) samples should be analyzed visually for water, dirt and other solids; (b) fuel should be clear and bright, not dirty or cloudy.
Standard Specification for Diesel Fuel Oils. (D-975).
A specification which references that “contamination levels in fuel can be reduced by storage in tanks kept free of water.”
Consumer Energy Council of America (CECA), National Fuels & Materials Research Consortium
2000 L Street, NW
Suite 802
Washington, DC 20036
202-659-0404
www.cecarf.org
National Fuels and Materials Research Consortium. Current (2003) research initiative. Ongoing research to maintain or improve heating oil fuel quality, including monitoring and preventative measures for water contamination throughout the fuel infrastructure, from transportation/distribution to storage.
Gas Technology Institute (GTI)
1700 S Mount Prospect Road
Des Plaines, IL 60018-1804
847-768-0500
www.gti.energy
Characterization of Microbial Communities in Gas Industry Pipelines. June 2003.
A technical study on microbial contamination pertaining to natural gas infrastructure.
AMPP
1440 S Creek Drive
Houston, TX 77084-4906
281-228-6200
www.ampp.org
Control of Internal Corrosion in Steel Pipelines and Piping Systems. (RP0175-75).
This Recommended Practice includes the mitigation and control of internal corrosion caused by moisture in a piping system, an often-overlooked component of a complete pipeline integrity program.
National Oilheat Research Alliance (NORA)
211 N Union Street, Suite 100
Alexandria, VA 22314
703-519-4204
www.noraweb.org
Oilheat Technician’s Manual. 2002.
A manual pertaining to the heating oil industry that includes guidelines for water monitoring and removal.
The Oilheat Research Program – Fuel Technology. Current (2003) research initiative.
Ongoing research into the issue of heating oil fuel quality during transportation and storage, including the development of field monitoring/test procedures for water and other quality indicators which service technicians can implement.
Petroleum Equipment Institute
PO Box 2380
Tulsa, OK 74101-2380
918-494-9696
www.pei.org
Recommended Practices for Installation of Underground Liquid Storage Systems. (RP100). 2000.
Provides information on engineering and construction practices with regard to the proper installation of underground liquid storage systems, including excavating, piping, cathodic protection, secondary containment, and other aspects of tank system installation.
Steel Tank Institute/Steel Plate Fabricators Association (STI/SPFA)
944 Donata Court
Lake Zurich, IL 60047
847-438-8265
www.stispfa.org
sti-P3® Cathodically Protected Underground Storage Tanks Installation Instructions (R821).
Installation instructions which include standard maintenance procedures for water monitoring and removal. These same procedures are outlined in all STI Installation Instructions:
-
- ACT-100® FRP Composite Steel Underground Storage Tanks (R913)
- ACT-100-U® Urethane Coated Steel Underground Storage Tanks (R971)
- PERMATANK® FRP Jacketed Steel Underground Storage Tanks (R923)
- F921® Double Wall Steel Aboveground Storage Tanks (R912)
- FIREGUARD® Lightweight Double-Wall Aboveground Storage Tanks (R912)
- FLAMESHIELD® Fire-Resistant Tanks (R912)
United States Department of Energy (DOE)
1000 Independence Ave., SW
Washington, DC 20585
202-586-5000
www.energy.gov
Maintenance and Storage of Fuel Oil for Residential Heating Systems. (BNL 48406). 2003.
Guideline addressing residential heating oil that includes recommendations to monitor the fuel during prolonged storage as “an essential part of maintaining good fuel quality…Contaminants in the old fuel, such as sludge and water in the tank, can degrade the quality of the new fuel.” BNL 48406 further recommends that “fuel specifications should become an integral part of the contractual agreements between the fuel supplier and the purchaser. In other words, a bulk sample of fresh fuel oil, used for heating, should at least meet all of the limits in specification ASTM D-396.”
United States Environmental Protection Agency (EPA)
Ariel Rios Building
1200 Pennsylvania Avenue, NW
Washington, DC 20460
202-272-0167
www.epa.gov/ust
Operating and Maintaining Underground Storage Tank Systems: Practical Help and Checklists (EPA 510-B-00-008). August 2000.
A booklet describing quality operations and maintenance practices compiled by State and Federal environmental regulators.
Resources
States
Check with your state authorities, commonly the Department of Weights and Measures, for regulations controlling the quantity of water allowed in fuel tanks at service stations.
Companies
The following companies are possible resources to contact for help on issues raised in this resource relating to water in storage systems, detection and removal, and treatment of microbial contamination (tank cleaning, biocides, etc.). Your local petroleum equipment supplier is always a good first point of contact. These companies are listed as a convenience only – the Steel Tank Institute/Steel Plate Fabricators Association does not endorse or have any interest in any of the following.
BCA, Inc.
(Microbial Contamination Control Services)
P.O. Box 3659
Princeton, NJ 08543-3659
609-716-0200
www.biodeterioration-control.com
Cim-Tek Filtration
201 N. Champaign Street
Bement, IL 61813
217-678-2511
www.cim-tek.com
Fuel Quality Services, Inc.
(MIC test kits and fuel additives)
P.O. Box 1380
Flowery Branch, GA 30542
770-967-9790
www.fqsinc.com
Mid-South Steel Products, Inc.
(Tank Cleaning Services)
2071 Corporate Circle
Cape Girardeau, MO 63703
800-325-8658
www.midsouthsteel.com
Mongoose Power Solutions
P.O. Box 13
1757 Route 9
Spofford, NH 03462
603-363-4842
www.mongoosepowersolutions.com
O’Day Equipment, Inc.
(Tank Cleaning Services)
P.O. Box 2706
Fargo, ND 58108
701-282-9260
www.odayequipment.com
Petroleum Recovery Services, LLC
4310 Amsterdam Street
North Charleston, SC 29418
843-225-1777
www.prsfuel.com
Tanknology, Inc.
8900 Shoal Creek Blvd
Bldg. 200
Austin, TX 78757
512-451-6334
www.tanknology.com
Resource Type
- Guidance
- Recommended Practice
Topic
- Aboveground
- Maintenance
- Underground