Awards
Product Awards
The STI/SPFA Fabricated Steel Product Awards recognize steel construction projects and products of member companies that exemplify the steel fabrication industry. These projects and products serve to bring attention to the positive qualities and flexibility of steel as the production material of choice for many industries.
Awards
Safety Diamond
Club Award
The Safety Diamond Club Award will be presented to any Fabricator or Affiliate member employer who has experienced the appropriate amount of work-hours or time worked without a recordable incident.
The following qualifications apply:
- 100+ Employees – 1,000,000 Work-hours
- 61-99 Employees – 650,000 Work-hours or 5 years
- 31-60 Employees – 450,000 Work-hours or 5 years
- 10-30 Employees – 250,000 Work-hours or 5 years

Safety Award of Excellence
The Safety Award of Excellence is presented to organizations whose employees have achieved a safety record with zero OSHA Recordable Incidents in the previous calendar year.
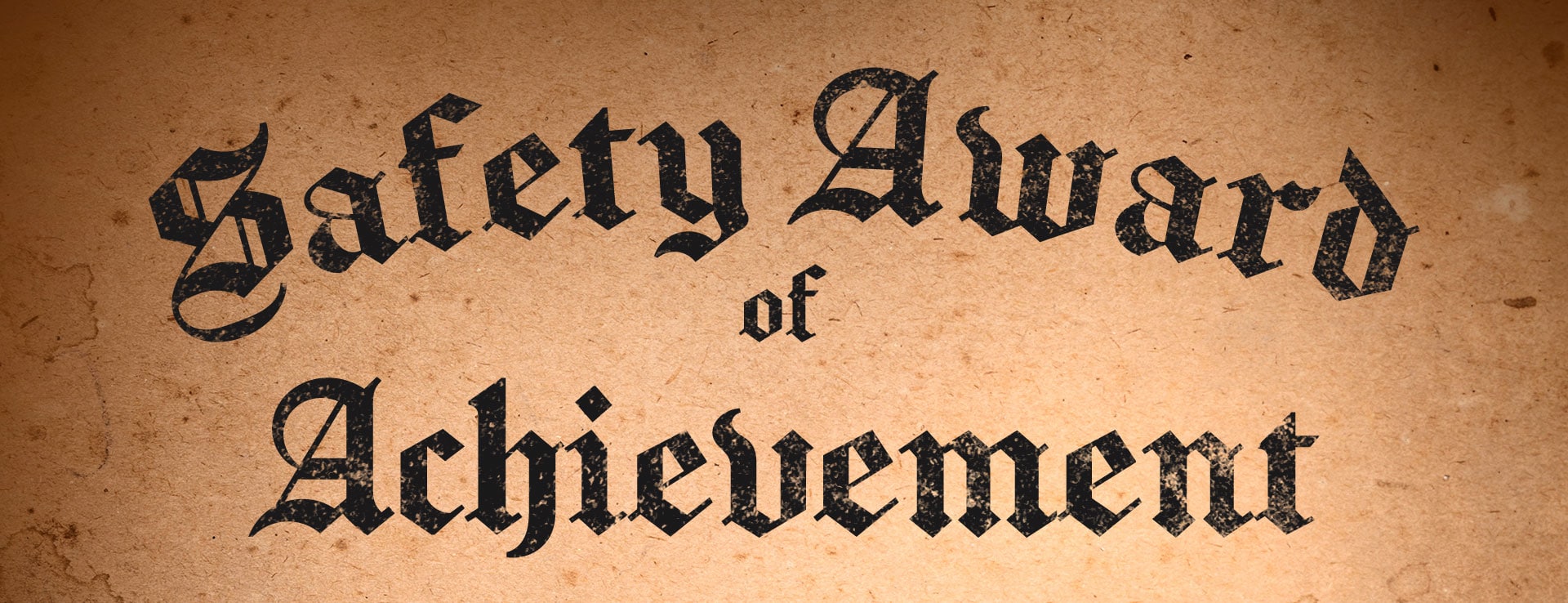
Safety Award of Achievement
Companies whose employees have achieved a minimum 10% reduction in the rate of OSHA Total Recordable Incidents, as compared with their average rate for the prior three years are eligible to receive the Safety Award of Achievement.
Awards
STI/SPFA Hall of Fame
The STI/SPFA Hall of Fame acknowledges individuals who have made exceptional contributions to STI/SPFA through volunteering, and who have worked tirelessly on behalf of the steel fabrication industry.
Awards
Patrick Kennedy
Leadership Award
The Patrick Kennedy Leadership Award recognizes individuals who exemplify leadership within STI/SPFA and the steel fabrication industry. Each year nominations are submitted and winners are selected by the Emerging Leaders Committee. Winners are announced during the STI/SPFA Fall Meeting.
Awards
Weld of the Year
The STI/SPFA Weld of the Year Awards recognize exemplary work of the talented craftspeople throughout the steel fabrication industry.